Return to:
Encyclopedia Home Page
Table of Contents
Author Index
Subject Index
Search
Dictionary
ESTIR Home Page
ECS Home Page
ELECTROCHEMICAL USES OF CARBON
Kim Kinoshita
Lawrence Berkeley National Laboratory
Berkeley, CA 94720, USA
(January, 2001)
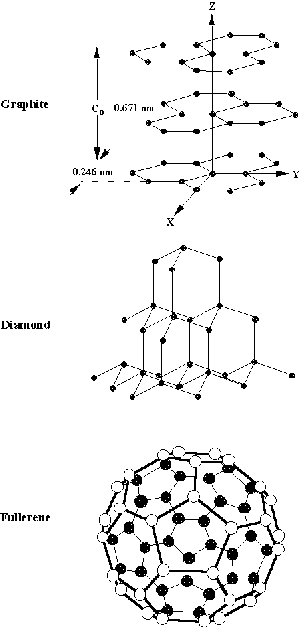 |
Fig. 1. Crystal structures of carbon. |
Carbon is one of the most abundant elements found on earth. It occurs freely in crystalline forms such as diamond and graphite. The crystal structures of these carbons are shown in Figure 1. The figure clearly shows that these carbons have two distinctly different structures. The diamond crystal is cubic, with the atoms arranged in a tetrahedral configuration. This arrangement of carbon atoms produces a solid that is the hardest known substance. Consequently, it is used as an industrial abrasive. In addition, diamond has a very high refractive index, hence it produces brilliant cut gems. Graphite, on the other hand, is soft, has a hexagonal structure, with the carbon atoms arranged in layer planes. The spacing between the layer planes in graphite is 0.3354 nm (nm = billionth of a meter). This layer structure facilitates easy cleavage along the planes, which makes it desirable as a solid lubricant. There are variations of the graphite structure. When the dimensions of the layer planes are small and the separation between the layer planes becomes large, the carbon is referred to as amorphous carbon (for example, charcoal, coke, and soot). Because of their difference in structures, diamond is an electrical insulator (although it can be made to conduct and used as a diamond electrode), whereas graphite is a good electrical conductor. The high conductivity of graphite and its good chemical stability are attractive features for its use in electrochemistry (see Table I below).
A more exotic form of carbon is the so-called "buckyball", discovered in 1985. It has a structure similar to a soccer ball. This discovery led to the 1996 Nobel Prize in Chemistry to H.W. Kroto, R.F. Curl, and R.E. Smalley. A typical structure of a buckyball (see Figure 1) contains 60 carbon atoms (C60) in a spherical structure consisting of 20 hexagons and 12 pentagons arranged on the surface. The more scientific name for this form of carbon is buckminsterfullerene (also called "fullerene"), so named for R. Buckminster Fuller (1895-1983) who developed the architectural structure know as the geodesic dome. This structure has a strong resemblance to the design of a soccer ball. The discovery of the buckyballs in 1985 has led to an expansion of research on C60 and variations of this structure. Evidence is available to show that buckyballs are present in nature, found in meteorite craters in Canada and New Zealand.
Manufacture and processing of carbon
Heating virtually any organic material or carbon-containing gases or liquids in an inert environment, which contains no oxygen, or in an environment with a limited supply of oxygen can produce carbon (that is, becomes carbonized). Soot is an example of a carbon that is produced in air where a limited supply of oxygen inhibits complete combustion. However, the type of carbon that is obtained depends strongly on the precursor that is carbonized. A terminology to identify carbons that are graphitizable (form graphite-like structures) or are non-graphitizable by heat treatment has been adopted. Hard carbons are those carbons that are non-graphitizable and are mechanically hard, hence the name. On the other hand, soft carbons are mechanically soft and can be graphitized. Hard carbons are obtained by carbonizing precursors such as thermosetting polymers (for example, phenol formaldehyde resins, furfuryl alcohol, and divinylbenzene styrene copolymer), cellulose, charcoal, and coconut shells. Transforming the solid precursor to solid carbon during the carbonization step usually forms hard carbons. One explanation for the inability of hard carbons to form a graphitic structure by heat treatment is the presence of strong crosslinking bonds which impede movement and re-orientation of the carbon atoms to form the ordered layer structure of graphite. Carbonizing precursors such as petroleum coke, oil, and coal-tar pitch form soft carbons. In these materials, the formation of carbon proceeds through an intermediate liquid-like phase (referred to as a mesophase), which facilitates the three-dimensional ordering that is necessary to create a graphite-like structure.
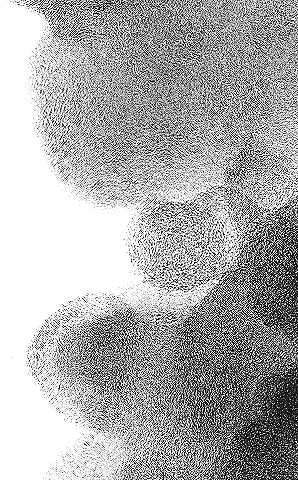 |
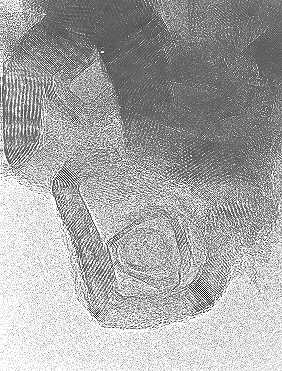 |
Fig. 2. High-resolution transmission electron micrographs of a carbon black before (top) and after (bottom) graphitization. |
The high-resolution transmission electron micrographs in Figure 2 show the structure of a carbon black before and after graphitization.
The micrograph on the top shows the amorphous structure of carbon black. No well-defined structure can be observed that would be indicative of the layer planes associated with graphite. However, after heating to 2800oC (5072oF) in an inert environment for 2 hours, the amorphous structure rearranges to form discrete layer planes indicative of graphite structure (micrograph on bottom). The distance between the layer planes near the surface of the particle approaches 0.3354 nm (nm = billionth of a meter), the theoretical value, but closer to the middle of the particle, only minimal changes occur. The reason for this difference in structure between the surface and interior of the particle can be explained as follows. Near the surface, the carbon atoms have more freedom of motion to rearrange. In the interior, motion is inhibited by the presence of the surrounding carbon atoms, and rearrangement to form the graphite layer structure becomes more difficult.
A carbon black called acetylene black, which is commonly used as an electrically conductive additive in batteries, is produced by the thermal decomposition of acetylene gas. The partially oxidative combustion of furnace oils, which are derived from petroleum refining, are also used to produce carbon blacks (furnace blacks). Other common organic materials such as wood, synthetic fibers, resins, and sugar are also precursors for carbon. One early starting material was charcoal, but it has been replaced by petroleum coke. When these materials are heated to produce carbon (carbonization), the chemical structure of the materials is destroyed and gases can form that contain carbon, oxygen, and hydrogen, depending on the original composition and ambient environment. The remaining solid product is mainly carbon.
Three common precursors of carbon are coke, petroleum coke, and coal-tar pitch. Coke is a solid, high in carbon content, that is produced by heating organic materials which has passed, at least in part, through a liquid or liquid-crystalline state during the carbonization process. Petroleum coke is a carbonization product of high-boiling hydrocarbon fractions (heavy residues) obtained in petroleum processing. It is the general term for all special petroleum coke products such as green, calcined, and needle petroleum coke. Coal-tar pitch is the residue produced by distillation or heat treatment of coal tar. It is a solid at room temperature, consists of a complex mixture of numerous predominantly aromatic hydrocarbons and heterocyclics, and exhibits a broad softening range instead of a defined melting temperature. Mixtures of coke and coal-tar pitch are heated to high temperature, usually above 2500oC (4532oF), to form solid carbon structures that are graphitic (that is, graphite-like).
Graphite is also found in nature. Natural graphite is classified as flake, vein, or microcrystalline (amorphous), depending on the crystallite size and particle shape. Major sources of natural graphite are found in Mexico, China, and Brazil. Flake graphite is anisotropic (that is, its properties depend on the crystallographic direction) and has crystallinity similar to that of single-crystal graphite. One problem with many sources of natural graphite is their high ash content (for example, iron, silicon), which can be as high as 25%. Much of this ash is removed by leaching in concentrated acid or exposure to halogen gases. Synthetic or artificial graphite is produced by heating a precursor carbon such as petroleum coke to temperatures in the range of 2800oC (5072oF) or higher.
A variety of amorphous carbons such as carbon black, active carbon, and glassy carbon are available. With the exception of glassy carbon, these amorphous carbons generally have high surface area, high porosity, and small particle size. Carbon blacks, for example, are available with surface areas that are >1000 m2/g, particle size <50 nm (nm = billionth of a meter), and density much less than the theoretical value for graphite (2.25 g/cm3). In addition, the morphology of carbon blacks may resemble individual spheres of about 250-nm diameter (that is, thermal blacks) or a cluster of fused carbon particles of <50-nm diameter (that is, furnace blacks). Active carbons are typically granular carbons that are produced by carbonizing materials such as wood (charcoal) coconut and other fruit shells, and low-rank coals. The resulting carbon is activated by treatment with gas (steam activation) or chemical processing. The end product is a carbon material with high surface area (>1000 m2/g) and extensive micropores (pore size <2 nm). It is this microporosity that contributes to the high adsorption properties, and is desirable for applications such as the removal of unwanted organic and inorganic species in water, elimination of noxious gases in air (for example, in gas masks), etc.
Properties of carbon
Table I. Desirable properties of carbon and |
graphite for electrochemical applications |
good electrical conductivity |
acceptable corrosion resistance |
availability in high purity |
low cost |
high thermal conductivity |
dimensional and mechanical stability |
light in weight and ease of handling |
availability in a variety of physical structures |
ease of fabrication into composite structures |
Carbonaceous materials have many desirable properties that have attracted their use in electrodes and other cell components for batteries, and these are summarized in Table I. Of practical importance is the contribution that is made by carbonaceous materials as an additive to enhance the electronic conductivity of the positive and negative electrodes. In other electrode applications, carbon serves as the electrocatalyst for electrochemical reactions and/or the substrate on which an electrocatalyst is located. In addition, carbonaceous materials are fabricated into solid structures that serve as the bipolar separator or current collector. Clearly, carbon is an important material for aqueous-electrolyte batteries. It would be very difficult to identify a practical alternative to carbon-based materials in many of the battery applications. The attractive features of carbon in electrochemical applications are its high electrical conductivity, acceptable chemical stability, and low cost. These characteristics are important for the widespread acceptance of carbon in electrochemistry.
Applications of carbon
The earliest uses of carbon may very well have been for writing and as a coloring agent. The starting carbon materials in these applications were most likely derived from soot. Only carbons with crystallographic structures related to graphite are found in commercial electrochemical applications. There is active research on buckyballs and their derivatives, but no viable commercial application of these carbons in electrochemistry has emerged.
Batteries
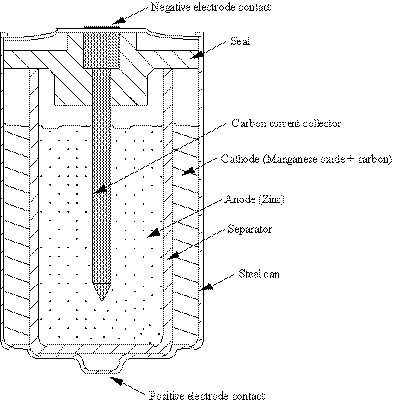 |
Fig. 3. Schematic representation of the cross-section of a typical alkaline-manganese dioxide cell. |
The role of carbon in electrochemistry probably started in 1792 with the discovery by Alessandro Volta (Italy) that charcoal could be substituted for metals in galvanic experiments (forerunner to the discovery of batteries). Perhaps the first practical application of carbonaceous materials in batteries was demonstrated in 1866 by Georges Leclanche in cells that bear his name. A more modern version of the Leclanche cell is the alkaline-manganese dioxide (MnO2) cell. A schematic representation of the cross-section of a typical alkaline cell, like the kind used in portable electronic devices, flashlights, etc., is shown in Figure 3.
The outer case is usually made of a thin metal sheet. Coarsely ground manganese dioxide is mixed with an equal volume of carbon to form the cathode (positive electrode). Carbon powders such as acetylene black and graphite are commonly used to enhance the conductivity of the positive electrodes in alkaline batteries. The particle morphology plays a significant role, particularly when carbon blacks are used in batteries as an electrode additive to enhance the electronic conductivity. One of the most common carbon blacks that are used as an additive to enhance the electronic conductivity of electrodes that contain metal oxides is acetylene black. A suitable carbon for this application should have characteristics that include: (i) low resistivity in the presence of the electrolyte and active electrode material, (ii) absorb and retain a significant volume of electrolyte without reducing its capability of mixing with the active material, (iii) exhibit compressibility and resiliency in the cell, and (iv) contain only low levels of impurities. Graphite has higher electrical conductivity than acetylene black but it is not capable of retaining the same volume of electrolyte or demonstrating the same mechanical properties in the cell. Acetylene black has a well-developed chain structure, and it is this characteristics which provides the capability to retain a significant amount of electrolyte. Acetylene black is capable of retaining over three times as much electrolyte (cm3 electrolyte/g carbon) as graphite, which has a very low structure. The capacity of Leclanche cells is dependent on the amount and type of carbon black that is used. Generally about 55 volume % carbon black mixed with manganese dioxide yields the maximum capacity. This composition agrees closely with the minimum in the electrical resistivity of the electrode mixture. The high electronic conductivity, chemical inertness and low cost are beneficial for the use of carbon for electrode materials in these batteries.
A carbon rod is used as a current collector for the positive electrode in cells. The carbon rod is made by heating extruded mixture of carbon (petroleum coke, graphite) and pitch that serves as a binder. A heat-treatment temperature of about 1100oC (2012oF) is used to carbonize the pitch and to produce a solid structure with low resistance. For example, heat treatment reduced the specific resistance from 1 to 0.0036 ohm cm and the density increased from 1.7 to 2.02 g/cm3.
Another example of the use of graphite as an additive to improve the electronic conductivity of an electrode can be found in the iron/nickel oxide (Fe/NiOOH) cell developed by Thomas Edison in the early 1900s. The positive electrode, which contained graphite (20-30% graphite flake), degraded rapidly during charge because of oxidation and swelling. This experience led to the development of electrolytic nickel flakes and eventually to the porous nickel plaque for use in nickel oxide electrodes.
One of the more exciting applications of carbon in batteries occurred in the early 1990's with the commercialization of lithium-ion cells by Sony Corporation. This development has led to a major expansion in the application of rechargeable lithium batteries for portable electronic devices such as cellular telephones, portable computers, camcorders, etc. Until the advent of the rechargeable lithium-ion cell, the only lithium cells that were commercially available were nonrechargeable batteries. The successful utilization of a carbon host to store lithium ions in the rechargeable negative electrode has led to the commercial development of lithium-ion cells. In commercial cells, the positive electrode is primarily a lithiated metal oxide, which also contains graphite to improve the electronic conductivity of the electrode.
The electrochemical reaction at the negative electrode in lithium-ion cells is the intercalation of lithium ions into graphite: the lithium ions in the electrolyte enter the space between the layer planes of graphite during charge. The distance between the graphite layer planes expands by about 10% to accommodate the lithium ions. The resulting material can be chemically represented as LixC6. When the cell is discharged, the lithium ions are removed from the graphite structure and return to the electrolyte. The maximum amount of lithium ions that is stored in graphite is equivalent to x = 1 (LiC6). Other carbons have been used which yield values of "x" that may be greater or less than one. One of the attractive features of this electrode is long cycle life that is observed when the reversible insertion and removal of lithium ions occur without mechanical degradation of the graphite structure. Currently, lithium-ion technology represents the most rapidly growing (in production volume) rechargeable battery system in the world.
Production of metals and chemicals
Carbon has played a major role in the industrial electrochemical production of many chemical materials, such as: chlorine and coustic, aluminum metal, and organic chemicals. Carbon is formed into solid structures that serve as the electrode sites where electrochemical reactions occur and products are formed. These carbon electrodes are formed by molding mixtures of graphite powder and pitch into solid pieces and then heating to high temperatures. The pitch is converted to carbon that holds the structure together. The development of artificial graphite in 1899 by the Acheson Graphite Co. located near Niagara Falls spurred the use of large graphite electrodes in the electrochemical production of chlorine, aluminum, and other chemicals. These graphite electrodes were a big improvement in performance and life over the amorphous carbons that were used in the electrodes. The graphite electrodes were capable of sustaining higher currents to increase production rates, and they were more corrosion resistant, and thermal-shock resistant. However, the electrodes are consumed and must be replaced periodically. For instance, 2 to 4 kg of carbon is consumed per metric ton of chlorine that is produced, and the life of the graphite electrode is only 6 to 24 months. The formation of carbon dioxide from graphite during chlorine production is responsible for the gradual consumption of the electrode. The situation is more dramatic for aluminum production where over 325 kg of carbon is consumed per ton of aluminum. In the case of chlorine production, metal oxide electrodes (ruthenium oxide + titanium oxide coating on titanium substrate) has essentially replaced graphite electrodes in commercial cells.
Fuel cells
Fuel cells are electrochemical devices that convert the chemical energy of a reaction directly into electrical and thermal energy. The traditional heat-engines (for example, steam turbines, internal combustion engines) that are used to generate electrical energy operate by the conversion route:
chemical energy ==> heat ==> mechanical motion ==> electricity
On the other hand, fuel cells follow the route:
chemical energy ==> electrochemical reaction ==> electricity
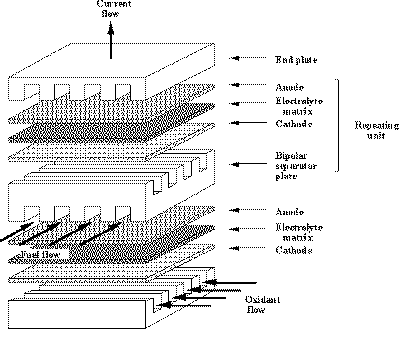 |
Fig. 4. Arrangement of the major cell components in a fuel cell stack. |
It is apparent from these routes that fuel cells produce electricity directly from reactions that eliminate the need for heat or mechanical processes. The key ingredient is the use of electrode materials that facilitate (catalyze) electrochemical reactions. In a typical fuel cell, gaseous fuels are fed continuously to the anode (negative electrode) compartment, and an oxidant (for example, oxygen from air) is fed continuously to the cathode (positive electrode) compartment; the electrochemical reactions take place at the electrodes to produce an electric current. The three major components that constitute the heart of a fuel cell are the fuel electrode (anode), oxygen electrode (cathode), and the electrolyte. These components are usually arranged in a stack, as illustrated in Figure 4. Each of these components are thin structures that may occupy an area approaching or even larger than a square meter, and have thickness of less than a fraction of a centimeter. A single cell consists of an anode, electrolyte and cathode, which is separated from the adjacent cell in the stack (series-connected) by a bipolar separator plate. The end plate serves for current collection. The fuel (typically a hydrogen-containing gas) and oxidant (typically oxygen from air) flow in small channels that may be part of the bipolar plate. Because the bipolar plate serves as part of the electron conduction path through the fuel cell stack, it must be electronically conductive, but it must not permit gas permeation. This configuration permits a fuel stack to be fabricated with over 400 cells arranged in series.
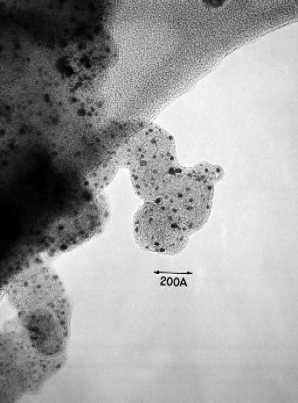 |
Fig. 5. High-resolution transmission electron micrograph platinum particles dispersed on carbon. |
Two major types of fuel cells rely heavily on carbon, usually in the form of graphitized carbon. These fuel cells are referred to as the phosphoric-acid fuel cell (PAFC) and the polymer-electrolyte-membrane fuel cell (PEMFC). The bipolar plate in these fuel cells may be a thin structure of machined graphite or molded graphite composite. The electrochemical reaction that occur between the fuel (hydrogen) and oxidant (oxygen) to generate electricity require costly metals such as metallic platinum, which is called an electrocatalyst. The electrochemical reactions occur on the surface of the electrocatalyst. Consequently, to minimize the amount of expensive metal electrocatalyst that is used, it is of major interest to increase the surface area of platinum available for reaction. This is achieved by preparing highly dispersed metal particles (that is, small particles) on carbon powder. An example of platinum particles dispersed on carbon is presented in the photograph (see Figure 5) obtained by transmission electron microscopy (TEM).
The platinum particles, which are about 2 nm (nm = billionth of a meter) in diameter, are evident as the solid black spots dispersed over the surface of larger and lighter particles of carbon. For TEM observations, the carbon particles are supported on a thin carbon film that appears as the mottled structure in the upper left-hand part of the micrograph. The surface area of the platinum is about 120 m2/g. If platinum particles of 1 nm in diameter were obtained, the surface area of platinum would be about 240 m2/g, thereby increasing the utilization of the platinum by 100%. Preparing such high-surface-area-supported electrocatalysts and maintaining the small particle size in the fuel cell are major technical challenges.
A fuel cell differs from the conventional battery in several respects. The battery is an energy storage device; that is, the maximum energy that is available is determined by the amount of chemical reactant stored in the battery itself. Thus, the battery will cease to produce electrical energy when the chemical reactants are consumed (that is, discharged). In a secondary battery, the reactants are regenerated during charge, which involves putting energy into the battery from an external source. The fuel cell, on the other hand, is an energy conversion device, which theoretically has the capability of producing electrical energy for as long as the fuel and oxidant are fed to the electrodes. In reality, degradation or malfunction of components limits the practical operating life of fuel cells.
The primary interest in PAFCs is for stationary power generation, whereas PEMFC's have attracted widespread interest for use in transportation applications. Without the availability of carbon as a reasonable stable and electronically conductive component, both the PAFC and the PEMFC would be even further from commercialization. Presently, cost is still a significant issue, but field tests of PAFCs have demonstrated that carbon meets the performance and life requirements in this application.
Double-layer capacitors
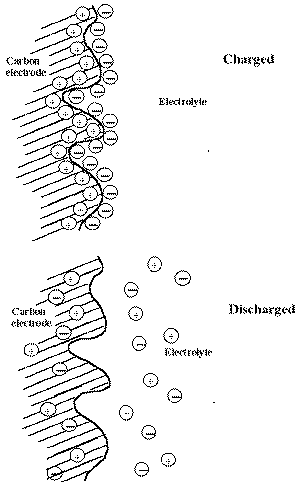 |
Fig. 6. Function of carbon electrode in an electrochemical capacitor. |
A capacitor is a passive electronic component that stores energy in the electrostatic field that is present at a two-phase interface (for example, solid/liquid or solid/solid). In its simplest form, a capacitor consists of two conducting plates separated by an insulating material called the dielectric. The capacitance is directly proportional to the surface areas of the plates, and is inversely proportional to the plates' separation. In a "double-layer capacitor" (also called an electrochemical capacitor), high-surface-area carbon (~1000 m2/g) serve as the two electrodes which are separated by a liquid electrolyte such as sulfuric acid contained in a thin layer of porous polymer membrane. Because carbon is available in high surface area, and because it is electronically conducting, it is an attractive material for use in capacitors. In addition, carbon is relatively stable in the capacitor environment.
The operating principle of a carbon electrode in an electrochemical capacitor is illustrated graphically in Figure 6. When a voltage is applied to the capacitor (and the capacitor is charged), the carbon electrodes attract positive or negative charges (that is, ions that carry the charges) to form double layers at the interfaces. (The figure shows only one electrode and the opposite arrangement of charges exist at the other carbon electrode.). The presence of these charged interfaces is the source of stored electrical energy, which when discharged releases electrons through the external circuit that is connected to the carbon electrodes. In the discharged state, the positive and negative ions are dissipated in the electrolyte and electrode. The major drawback of carbon as an electrode material is its high resistivity because of the poor particle-to-particle contact between the small carbon particles that provide the high surface area. The high resistivity limits the charge/discharge rates. Typical applications include back-up power for small computers and memory devices.
The distinction between a battery and electrochemical capacitor is not clear-cut. A battery relies on electrochemical reactions that involve active materials in the electrode. In this case, active means that the materials participate in the reaction, and a transfer of electrons between the active material and ionic species in solution occurs across the solid/liquid interface. On the other hand, in an "ideal" electrochemical capacitor that utilizes carbon, the electrodes play a passive role. That is, the electrode surface only participates by serving as sites for charged species to accumulate and no electron transfer occurs across the solid/liquid interface. While in a "practical" electrochemical capacitor there may occur some surface oxidation/reduction on the electrodes, that is, it operates partly as a capacitor, partly as a battery.
Concluding remarks
Carbon plays an indispensable role in our daily lives. For example, automobile tires contain a large fraction of carbon black to reinforce rubber. The carbon improves wear and abrasion resistance to extend the usable life of the tire. The rubber industry consumes about 90% of the total production of carbon blacks, with nearly 2/3 of that used in tires. Carbon black is used in plastics because it imparts ultra-violet protection, enhanced conductivity, and reinforcement to the structure. Plastic pipes, electrical cables, and anti-static shielding are other materials that rely on carbon blacks as an integral component. In the last half of the 20th century, developments in photocopying (xerography) and printing (ink-jet and laser printers) have led to a growing market for carbon blacks. The carbon particles used in toners are about 10 microns (millionth of a meter) in diameter. Activated carbons play a major role in purification of water, food, pharmaceuticals, and fine chemicals. Their high surface area and high porosity are ideal for adsorbing and removing unwanted impurities. As a final example, carbon fibers are finding increased applications in sporting goods (golf clubs, tennis rackets) and aerospace because they are lightweight and improve mechanical strength. The overall consumption of carbon in electrochemical applications, in contrast to those mentioned above, is relatively small, with aluminum refining being a major user of graphite electrodes.
Related articles
Carbon is used in many industrial electrolytic processes:
Aluminum production
Brine electrolysis
Industrial organics
and in
Batteries
Fuel cells
PEM fuel cells
Bibliography
- Advanced Anode Materials for Li-Ion Batteries, K. Kinoshita, in "New Trends in Electrochemical Technology: Energy Storage Systems for Electronics" pp 193-251, T. Osaka and M. Datta (editors), Gordon and Breach, Reading, UK, 1999.
- Introduction to Carbon Technologies, H. Marsh, E. A. Heintz, and F. Rodrigues-Peinoso (editors), University of Alicante, Spain, 1997.
- Fuel Cells and Their Applications, K. Kordesch and G. Simader, VCH, Deerfield Beach, FL, 1996.
- Microstructure, Morphology and General Physical Properties, W. M. Hess and C. R. Herd, in "Carbon Black: Science and Technology (second edition)" pp 89-173, J.-B. Donnet, R. C. Bansal, and M.-J. Wang (editors), Marcel Dekker, New York, 1993.
- Electrochemical Oxygen Technology, K. Kinoshita, Wiley, New York, 1992.
- Fuel Cell Handbook, A. J. Appleby and F. R. Foulkes, Van Nostrand Reinhold, New York, 1989.
- Carbon: Electrochemical and Physicochemical Properties, K. Kinoshita, Wiley, New York, 1988.
Listings of electrochemistry books, review chapters, proceedings volumes, and full text of some historical publications are also available in the Electrochemistry Science and Technology Information Resource (ESTIR). (http://knowledge.electrochem.org/estir/)
Return to:
Top
Encyclopedia Home Page
Table of Contents
Author Index
Subject Index
Search
Dictionary
ESTIR Home Page
ECS Home Page
|