Return to:
Encyclopedia Home Page
Table of Contents
Author Index
Subject Index
Search
Dictionary
ESTIR Home Page
ECS Home Page
SOLID OXIDE FUEL CELLS
Subhash C. Singhal
Pacific Northwest National Laboratory
PO Box 999
Richland, WA 99352-0999, USA
(March, 2008)
Solid oxide fuel cells (SOFCs) offer
a clean, low-pollution technology
to electrochemically generate
electricity at high efficiencies; since
their efficiencies are not limited the
way conventional heat engine's is. These
fuel cells provide many advantages over
traditional energy conversion systems
including high efficiency, reliability,
modularity, fuel adaptability, and very
low levels of polluting emissions.
Quiet, vibration-free operation of
SOFCs also eliminates noise usually
associated with conventional power
generation systems.
Up until about six
years ago, SOFCs were being developed
for operation primarily in the
temperature range of 900 to 1000oC (1692 to 1832oF); in
addition to the capability of internally
reforming hydrocarbon fuels (for example,
natural gas), such high temperature
SOFCs provide high quality exhaust
heat for cogeneration, and when
pressurized, can be integrated with
a gas turbine to further increase the
overall efficiency of the power system.
However, reduction of the SOFC
operating temperature by 200oC (392oF) or
more allows use of a broader set of
materials, is less demanding on the seals
and the balance-of-plant components,
simplifies thermal management, aids
in faster start up and cool down, and
results in less degradation of cell and
stack components. Because of these
advantages, activity in the development
of SOFCs capable of operating in the
temperature range of 650 to 800oC (1202 to 1472oF) has
increased dramatically in the last few
years. However, at lower temperatures,
electrolyte conductivity and electrode
kinetics decrease significantly;
to overcome these drawbacks,
alternative cell materials and designs
are being extensively investigated.
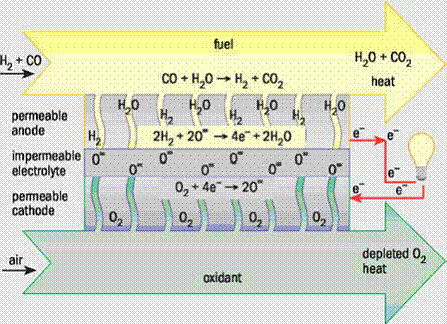 |
Fig. 1. Operating principle of a solid oxide fuel cell. |
An SOFC essentially consists of two
porous electrodes separated by a dense,
oxide ion conducting electrolyte. The
operating principle of such a cell is
illustrated in Figure 1. Oxygen supplied at
the cathode (air electrode) reacts with
incoming electrons from the external
circuit to form oxide ions, which
migrate to the anode (fuel electrode)
through the oxide ion conducting
electrolyte. At the anode, oxide ions
combine with hydrogen (and/or carbon monoxide) in the fuel
to form water (and/or carbon dioxide), liberating
electrons. Electrons (electricity)
flow from the anode through the
external circuit to the cathode.
The materials for the cell components are
selected based on suitable electrical
conducting properties required of these
components to perform their intended
cell functions; adequate chemical and
structural stability at high temperatures
encountered during cell operation as
well as during cell fabrication; minimal
reactivity and interdiffusion among
different components; and matching
thermal expansion among different
components.
Materials and cell designs
Yttrium-doped zirconium oxide (YSZ) remains
the most widely used material for the
electrolyte in SOFCs because of its
sufficient ionic conductivity, chemical
stability, and mechanical strength.
The only drawback of stabilized YSZ
is the low ionic conductivity in the
lower cell operation temperature regime,
below about 750oC (1382oF). Two solutions
that have been tried to resolve this
problem are to decrease the thickness
of the YSZ electrolyte and to find other
materials to replace the yttrium. Scandium-doped
zirconium oxide has higher conductivity than
YSZ but high cost of scandium and
detrimental ageing effects in scandium doped
zirconium oxide make it less attractive in
commercializing SOFCs. Gadolinium- or
samarium-doped cerium oxide materials possess
higher oxide ion conductivity
compared to zirconium based materials. However, cerium oxide based
materials, under reducing conditions at
high temperatures, exhibit significant
electronic conductivity and dimensional
change. Operation at temperatures
below about 600oC (1112oF) overcomes this
problem, and cerium oxide based materials are
successfully being used as electrolyte
in SOFCs by Ceres Power Limited (UK).
In addition to the traditionally used
oxides of zirconium
and cerium, other mixed oxides also provide an opportunity to develop
oxide ion conducting electrolytes.
One mixture, containing among others gallium oxide, has attracted attention as an electrolyte.
However, it has two drawbacks: uncertain
cost of gallium, and uncertain chemical
and mechanical stability of the oxide. In
spite of these drawbacks, Mitsubishi
Materials Corporation (Japan) is using
this as the electrolyte in its SOFCs
and has successfully built and tested up
to 10-kW size SOFC power systems.
The oxidant gas is air or oxygen at the
SOFC cathode, and the electrochemical
reduction of oxygen requires a series of
elementary reactions and involves the
transfer of multiple electrons. The SOFC
cathode must meet the requirements
of high catalytic activity for oxygen
molecule dissociation and oxygen
reduction, high electronic conductivity,
chemical and dimensional stability
in environments encountered during
cell fabrication and cell operation,
thermal expansion match with other
cell components, and compatibility and
minimum reactivity with the electrolyte
and the interconnection. Finally, the
cathode must have a stable, porous
microstructure so that gaseous oxygen
can readily diffuse through the cathode
to the cathode/electrolyte interface.
These stringent electrochemical and
mechanical requirements greatly
restrict the number of suitable candidate
materials.
Lanthanum manganite,
which, when substituted with low valence
elements such as calcium or strontium,
has good electronic conduction. Moreover, it
possesses adequate electrocatalytic
activity, a reasonable thermal expansion
match to YSZ, and stability in the
SOFC cathode operating environment.
For SOFCs operating at substantially
lower temperatures, such as 650 to
800oC (1202 to 1472oF), alternative cathode materials,
typically containing transition
metals such as cobalt, iron, and/or nickel, have been developed and
optimized for better performance. In
general, these materials offer higher
oxide ion diffusion rates and exhibit
faster oxygen reduction kinetics at the
cathode/electrolyte interface compared
with lanthanum manganite. However,
the thermal expansion coefficient of
cobaltites is much higher than that of
the YSZ electrolyte, and the electrical
conductivities of ferrites and nickelites
are low. Nevertheless, promising
results have been reported using these
materials, though in many cases the
improved cathodic performance is found
to decrease during the cell lifetime as a
result of chemical or microstructural
instability. Minimization of cathodic
polarization losses is one of the biggest
challenges to be overcome in obtaining
high, stable power densities from lower
temperature SOFCs. However, these materials are very reactive toward
YSZ. Therefore, a thin layer, generally
of a cerium oxide based material, is used to
reduce the chemical reaction between
the cathode and YSZ. Microstructure
also plays a major role in the cathode
polarization; this is particularly true
when a composite cathode, which shows a
better performance compared to a single
composition cathode, is used. It has been shown that polarization
resistance depends upon the grain size
of the ionic conductor in the composite
electrode and the volume fraction of
porosity.
The anode must be an excellent
catalyst for the oxidation of fuel (hydrogen, carbon dioxide),
stable in the reducing environment of
the fuel, electronically conducting, and
must have sufficient porosity to allow the
transport of the fuel to and the transport
of the products of fuel oxidation away
from the electrolyte/anode interface
where the fuel oxidation reaction takes
place. The other requirements include
matching of its thermal expansion
coefficient with that of the electrolyte
and interconnect; integrity of porosity
for gas permeation; chemical stability
with the electrolyte and interconnect;
and applicability to use with versatile
fuels and impurities. In addition, cost
effectiveness is always a factor for
commercialization.
Nickel-YSZ composites
are the most commonly used anode
materials for SOFCs. Nickel is an excellent
catalyst for fuel oxidation; however,
it possesses a high thermal expansion
coefficient, and exhibits
coarsening of microstructure due to
metal aggregation through grain growth
at cell operation temperatures. YSZ in
the anode constrains nickel aggregation
and prevents sintering of the nickel
particles, decreases the effective thermal
expansion coefficient bringing it closer
to that of the electrolyte, and provides
better adhesion of the anode with the
electrolyte. In these anodes,
nickel has dual roles of the catalyst for
hydrogen oxidation and the electrical
current conductor. In addition, it is also
highly active for the steam reforming
of methane. This catalytic property
is exploited in the so-called internal
reforming SOFCs that can operate on
fuels composed of mixtures of methane
and water. Although nickel is an excellent
hydrogen oxidation and methane-steam reforming
catalyst, it also catalyzes the
formation of carbon from hydrocarbons
under reducing conditions. Unless
sufficient amounts of steam are present
along with the hydrocarbon to remove
carbon from the nickel surface, the
anode may be destroyed. As a result,
even when using methane as the fuel,
relatively high steam-to-carbon ratios
are needed to suppress this deleterious
reaction. Unfortunately, due to the
high catalytic activity of nickel for
hydrocarbon cracking, this approach
does not work for higher hydrocarbons,
and it is generally not possible to
operate nickel-based anodes on higher
hydrocarbon-containing fuels without
pre-reforming with steam or oxygen.
In spite of this drawback, nickel-YSZ
composite remains the most commonly
utilized anode material for SOFCs and is
satisfactory for cells operating on clean,
reformed fuel.
However, advanced SOFC
designs place additional constraints
on the anode, such as tolerance of
oxidizing environments and/or the
ability to tolerate significant quantities
of sulphur and/or hydrocarbon species
in the fuel stream. Alternative materials,
such as cerium oxide or strontium
titanate/cerium oxide mixtures, have yielded some
promising results in these designs,
but the benefits obtained in terms of
sulphur, hydrocarbon and/or redox
tolerance are counterbalanced by other
limitations (such as the difficulty of
integrating such materials with existing
cell and stack fabrication processes and
materials). Copper based anodes have
also been proposed for intermediate temperature
(<800oC; <1472oF) SOFCs intended
to operate directly on hydrocarbon
fuels without prior reformation,
but the lack of catalytic activity
for oxidation of fuel in copper and
sintering of copper at the cell operating
temperatures have limited their use
in practical SOFCs.
Since a single cell only produces
voltage less than 1 V and power
around 1 W/cm2, many cells are
electrically connected together in a
cell stack to obtain higher voltage
and power. To connect multiple cells
together, an interconnection is used in
SOFC stacks. The requirements of the
interconnection are the most severe of
all cell components and include: nearly
100 percent electronic conductivity;
stability in both oxidizing and reducing
atmospheres at the cell operating
temperature since it is exposed to air (or
oxygen) on the cathode side and fuel
on the anode side; low permeability
for oxygen and hydrogen to minimize
direct combination of oxidant and
fuel during cell operation; a thermal
expansion coefficient close to that of
the cathode and the electrolyte; and
non-reactivity with other cell materials.
To satisfy these requirements, doped
lanthanum chromite is used as the
interconnection for cells intended for
operation at about 1000oC (1832oF).
In cells intended for operation at lower
temperatures (<800oC; <1412oF), it is possible
to use oxidation-resistant metallic
materials for the interconnection.
Compared to lanthanum chromite
ceramic interconnects, metallic alloys
offer advantages such as improved
manufacturability, significantly lower
raw material and fabrication costs,
and higher electrical and thermal
conductivity. But to be useful for
the interconnect application, the
metallic alloys must satisfy additional
requirements, including resistance
to surface oxidation and corrosion
in a dual atmosphere (simultaneous
exposure to oxidizing and reducing
atmospheres), thermal expansion
matching to other stack components
(particularly for stacks using a rigid
seal design), chemical compatibility
with other materials in contact with
the interconnect, such as seals and cell
materials, high electrical conductivity
not only through the bulk material
but also in in-situ-formed oxide scales,
mechanical reliability and durability
at the cell operating temperature, and
strong adhesion between the as-formed
oxide scale and the underlying alloy
substrate. Ferritic stainless steels are
the most promising candidates, owing
to the fact that some alloys in this
family offer a protective and conductive
chromium-based oxide scale, appropriate
thermal expansion behavior, ease of
manufacturing and low cost. Several new
ferritic stainless steels have been developed
specifically for SOFC interconnects.
Although these alloys demonstrate
improved performance over traditional
compositions, several critical issues
remain; among these are chromium oxide scale
evaporation and subsequent poisoning
of cathodes; scale electrical resistivity
in the long term; corrosion and spalling
under interconnect exposure conditions;
and compatibility with the adjacent
components such as seals and electrical
contact layers. To overcome some of
these problems, some surface coatings can be applied
onto metallic interconnects to minimize
scale growth, electrical resistance and
chromium volatility.
Stack design
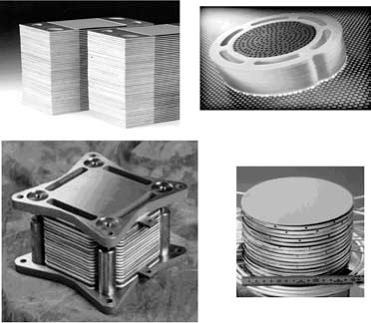 |
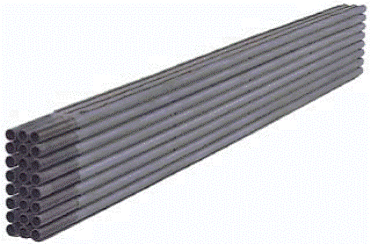 |
Fig. 2. Illustration of planar cell stacks (top) and a tubular cell bundle (bottom). |
In terms of stack design, most
development has focused on planar
and tubular design cells, each of these
designs having a number of interesting
variants; for example, the planar SOFC
may be in the form of a circular disk
fed with fuel from the central axis, or it
may be in the form of a square plate fed
from the edges. The tubular SOFC may
be of a large diameter (>15 mm), or of
much smaller diameter (<5 mm), the
so-called microtubular cells. Also, the
tubes may be flat and joined together
to give higher power density and easily
printable surfaces for depositing the
electrode layers. Figure 2 illustrates
typical planar cell stacks and a
tubular cell bundle. One of the inherent
advantages of tubular cell bundles is
that the air and the fuel are naturally
isolated because the tubes are closed at
one end.
However, in the case of planar
cell stacks, an effective seal must be
provided to isolate air from the fuel.
The seal must have a thermal expansion
match to the fuel cell components,
must be electrically insulating and must
be chemically stable under the
operational conditions of the stack. Also,
the seal should exhibit no deleterious
interfacial reactions with other cell
components, should be stable under
both the high temperature oxidizing
and reducing operational conditions,
should be created at a low enough
temperature to avoid damaging cell
components (under 850oC or 1562oF for some
materials), and should not migrate or
flow from the designated sealing region
during sealing or cell operation. In
addition, the sealing system should
be able to withstand thermal cycling
between the cell operation temperature
and room temperature. A number of
different sealing approaches are under
development, including rigid, bonded
seals (for example, glass-ceramics and brazes),
compliant seals (for example viscous glasses)
and compressive seals (for example, mica-based
composites); multiple sealants may also
be used in any given stack design between
different cell components. Successful
development of sealing materials and
concepts for planar SOFCs is probably
the most important issue for the long-term
performance stability and lifetime
of planar SOFC stacks and hence
for their eventual commercialization at
competitive costs.
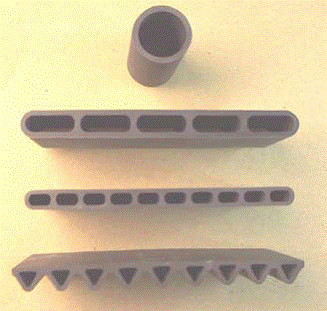 |
Fig. 3. Alternate tubular geometry cells being developed by Siemens. |
The single biggest advantage of
tubular cells over planar cells is that they
do not require any high temperature
seals to isolate oxidant from the fuel,
and this makes performance of tubular
cell stacks very stable over long periods
of times (several years). However, their
areal power density is much lower
(about 0.2 W/cm2) compared to planar
cells (up to 2 W/cm2 for single cells
and at least 0.5 W/cm2 for stacks)
and manufacturing costs higher. The
volumetric power density is also lower
for tubular cells than for planar cells.
To increase the power density and
reduce the physical size and cost of
tubular SOFC stacks, alternate tubular
geometry cells, as illustrated in Figure 3,
are under development by Siemens.
Such alternate geometry cells combine
all the advantages of the tubular SOFCs,
such as not requiring high temperature
seals, while providing higher areal
and volumetric power densities. The
performance of these new design cells is
higher than that of cylindrical tubular
cells, but still lower than that of anode-supported planar cells.
Applications
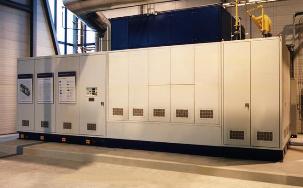 |
Fig. 4. A Siemens Westinghouse 100 kilowatt SOFC power system. |
Using planar SOFCs, stationary power
generation systems of from 1-kW to 25-kW
size have been fabricated and tested by
several organizations. Several hundred 1-kW size combined heat and power
units for residential application were field
tested by Sulzer Hexis; however, their
cost and performance degradation was
high and stack lifetime too short. With
improved sealing materials and sealing
concepts, planar SOFC prototype systems
in the 1- to 5-kW sizes have recently been
developed and are being tested by various
organizations with greater success. Using
tubular (cylindrical) SOFCs, Siemens/
Westinghouse fabricated a 100-kW
atmospheric power generation system (Figure 4).
The system was successfully operated
for two years in the Netherlands on
desulfurized natural gas without any
detectable performance degradation. It
provided up to 108 kW of ac electricity
at an efficiency of 46% to the Dutch grid
and approximately 85 kW of hot water
for the local district heating system. At
the conclusion of the operation in The
Netherlands, the system was moved to a
German utility site in Essen, Germany,
where it operated successfully for
another 4,000 hours. After replacing
some cells, the system was then installed
and operated in Italy, for over two years,
again with very stable performance.
Siemens/Westinghouse tubular cells
have also been used to fabricate and field
test over a dozen 5-kW size combined heat and power units,
each about the size of a refrigerator.
These units gave excellent performance
and performance stability on a variety of
hydrocarbon fuels. However, at present,
their cost is high; future such units are
expected to use higher power density
alternate tubular geometry cells to drive
down the cost.
Another application of SOFC systems
is in the transportation sector. The polymer electrolyte membrane fuel cell
is generally regarded as the
fuel cell of choice for transportation
applications. These
fuel cells require pure
hydrogen, with no carbon monoxide, as the fuel to operate
successfully. However, presently no
hydrogen infrastructure exists, and on-board
reformer systems to produce hydrogen from
existing fuel base (gasoline, diesel) are
technically challenging, complex, and
expensive. Furthermore, it is difficult
to eliminate the carbon monoxide entirely from the
reformate stream. In contrast, SOFCs
can use carbon monoxide along with hydrogen as fuel, and
their higher operating temperature and
availability of water on the anode side
makes on-cell or in-stack reformation of
hydrocarbon fuels feasible. Also, no noble
metal catalysts are used in SOFCs reducing
cost of the cells. The initial application
of SOFCs in the transportation sector
will be for on-board auxiliary power
units. Such auxiliary power units, operating on
existing fuel base, will supply the ever increasing
electrical power demands
of luxury automobiles, recreational
vehicles, and heavy-duty trucks. Delphi
Corporation has developed a 5-kW auxiliary power unit
using anode-supported planar SOFCs.
This unit is intended to operate on
gasoline or diesel, which is reformed
through catalytic partial oxidation. The
building blocks of such an auxiliary power unit consist of
an SOFC stack, fuel reformation system,
waste energy recovery system, thermal
management system, process air supply
system, control system, and power
electronics and energy storage (battery)
system. Delphi has reduced the mass and
volume in successive generation auxiliary power units to meet the stringent automotive
requirements; the remaining issues of
start up time and tolerance to thermal
cycling are presently being worked on.
Summary
The challenge in successfully
commercializing SOFCs offering high
power densities and long term durability
requires reduction of costs associated
with the cells and the balance-of-plant.
Additionally, for transportation auxiliary power unit
applications, ability for rapid start up and
thermal cycling needs to be developed.
Acknowledgement
This article was reproduced from the The Electrochemical Society Interface (Vol. 16, No. 4, Winter 2007) with the permission of The Electrochemical Society, Inc. (ECS) and the author.
Related articles
Batteries
Current density distribution in electrochemical
cells
Fuel cells
Micro fuel cells
PEM fuel cells
Bibliography
- Solid Oxide Fuel Cells 10 (SOFC-X) (Electrochemical Society Transactions, Vol. 7, No. 1), K. Eguchi, S. C. Singhal, H. Yokokawa, and J. Mizusaki (editors), ECS, Pennington, NJ, 2007.
- Advanced Anodes for High-Temperature Fuel Cells, A. Atkinson, S. Barnett, R. J. Gorte, J. T. S. Irvine, A. J. McEvoy, M. Mogensen, S. C. Singhal, and J. Vohs, "Nature Materials" Vol. 3, No. 1, pp 17-27, 2004.
- U.S. Distributed Generation Fuel Cell Program, M. C. Williams, J. P. Strakey, and S. C. Singhal, "Journal of Power Sources" Vol. 131, pp 79-85, 2004.
- High Temperature Solid Oxide Fuel Cells: Fundamentals, Design and
Applications, S. C. Singhal and K. Kendall (editors), Elsevier, Oxford, 2003.
- Solid Oxide Fuel Cells for Stationary, Mobile, and Military Applications, S. C. Singhal, "Solid State Ionics" Vol. 152-153, pp 405-410, 2002.
- Science and Technology of Solid Oxide Fuel Cells, S. C. Singhal, "Materials Research Bulletin" Vol. 25, pp 16-21, 2000.
- Advances in Solid Oxide Fuel Cell Technology, S. C. Singhal, "Solid State Ionics" Vol. 135, pp 305-313, 2000.
Listings of electrochemistry books, review chapters, proceedings volumes, and full text of some historical publications are also available in the Electrochemistry Science and Technology Information Resource (ESTIR). (http://knowledge.electrochem.org/estir/)
Return to:
Top
Encyclopedia Home Page
Table of Contents
Author Index
Subject Index
Search
Dictionary
ESTIR Home Page
ECS Home Page
|